Desert woodworking – FineWoodworking
Initially titled “Desert Cabinetry” in Nice Woodworking #3—Summer season 1976
The local weather of the desert US Southwest can have a devastating impact on furniture. Individuals shifting there from the East usually watch their antiques, which have survived a whole lot of years in a comparatively humid local weather, break up earlier than their eyes. Cabinetmakers undergo comparable discouragement. It’s uncommon to seek out even skilled cabinetmakers who haven’t had items ruined by cracks or damaged joints.
The risks of humidity, or lack thereof
As atmospheric situations change, wooden expands or contracts till an equilibrium moisture content material is reached. Furnishings from the East Coast has an equilibrium moisture content material of twelve to fifteen p.c. When this furnishings is dropped at the Southwest, its equilibrium moisture content material could lower to 6 p.c with vital shrinkage ensuing. Regular Midwestern hardwoods are kiln-dried to roughly twelve p.c. When that lumber is shipped to the Southwest, the moisture content material will lower and trigger shrinkage. Moreover, seasonal humidity and temperature modifications have an effect on the moisture content material of the wooden and trigger motion, which can lead to shrinkage, growth, distortion (resembling cupping, warping, bowing, or springing), and even splitting.
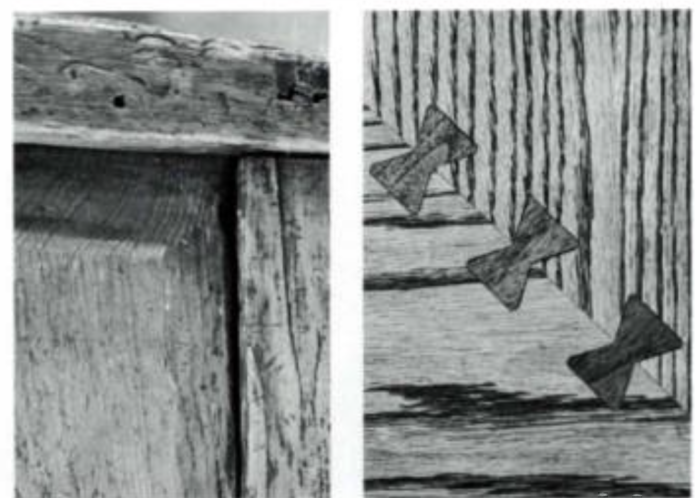
Wooden strikes totally different quantities in several instructions. Lengthwise transferment is negligible. Nonetheless, radial motion is critical, and circumferential (or tangential) motion is roughly fifty p.c better than radial motion. Due to this fact, joints between finish grain and edge grain, and between plainsawn lumber (with tangential motion throughout its face) and quartersawn lumber (with radial motion throughout its face) will probably be topic to vital stress upon modifications in wooden moisture content material. (The identical can also be true within the lamination of various kinds of wooden with different motion traits.) This stress generates super forces which might break joints and cut up wooden.
A wealthy historical past
Many cabinetmaking strategies used to reduce wooden motion could be seen in New Mexican Spanish Colonial furnishings (hereafter, Spanish Colonial furnishings). Trendy Spanish Colonial furnishings is the embodiment of a desert cabinetmaking custom stretching again for hundreds of years. The Arabs from Syria and Egypt and the Berbers from Northwestern Africa (collectively referred to as the Moors) launched designs and strategies from their homeland throughout their lengthy occupation of Spain. By the start of the seventeenth century when colonists supplanted Conquistadores in New Mexico, the Spanish Moorish furnishings design confluence had produced the favored mudejar fashion.
Though most colonists took little or no furnishings with them, they did imitate the normal and mudejar designs standard in Spain after they left. Their designs and execution have been cruder than Spanish renditions and in native pine relatively than the normal Spanish hardwoods (largely walnut). Nonetheless, they included most of the cabinetmaking strategies utilized by the Spanish and Moors earlier than them. The relative isolation of New Mexico and the truth that the unique designs produced easy furnishings that held up effectively underneath the pains of frontier life enabled Spanish Colonial furnishings design to endure for a whole lot of years.
Even immediately, in small villages throughout northern New Mexico, native craftsmen use the identical furnishings designs and strategies as their forefathers. Within the bigger cities and cities this identical fundamental design and building, usually supplemented with Spanish and Mexican design and trendy strategies, is utilized in business manufacturing.
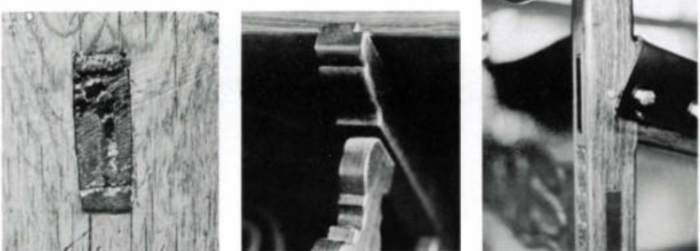
Doweled joints
One of the conspicuous building strategies in Spanish Colonial furnishings is the doweled mortise-and-tenon joint. After all, the mortise-and-tenon weren’t used merely to accommodate wooden transferment. Till the event of doweled joints, the mortise-and-tenon joint was the one one to make use of in lots of kinds of positive joinery. Nor would it not be correct to say that the doweling of the tenon is solely a desert cabinetmaking approach. It was utilized in positive furnishings in lots of nations and was thought-about the most effective insurance coverage in opposition to joint breakage from any trigger. For no matter motive the doweled mortise-and-tenon joint was utilized in different nations, it does seem possible that its nearly common use in Spanish Colonial furnishings and its continuation after digital abandonment elsewhere is not less than partly attributable to its potential to carry tight even when the glue joint is damaged by shrinkage. The becoming a member of of edge grain to finish grain is often the purpose of best weak point and susceptibility to wooden motion injury in furnishings building.
A attribute function of the Spanish Colonial doweled mortise-and-tenon is the virtually unique use of just one dowel. European and American cabinetmakers usually used two dowels at both aspect of the tenon to extend the energy of the joint. The absence of this further dowel in most Spanish Colonial furnishings is probably attributable to the truth that shrinkage throughout the face of the tenon will trigger stress to construct up between the 2 dowels and cut up the tenoned piece. Using just one dowel prevents such stress from creating.
Wedged tenons
One other attribute of this joint, though seldom seen immediately, is the wedged tenon. Historically the wedges have been pushed in on the fringe of the tenon. This compression of the pine tenon minimized loosening of the joint by shrinkage. To wedge the tenon with the crude instruments that they had, the New Mexicans broke with the virtually common Spanish custom of utilizing blind tenons and commenced chopping most mortises by. Trendy makers of Spanish Colonial furnishings have continued to make use of the by tenon for stylistic causes although the primary motive for its use, ease of tenon wedging, has been largely deserted tenon is the virtually unique use of just one dowel. European and American cabinetmakers usually used two dowels at both aspect of the tenon to extend the energy of the joint.
Eradicating tenons
The absence of offset tenon doweling is typically used within the Spanish Colonial doweled mortise-and-tenon joint. The dowel gap is bored by the mortised piece (with a waste piece inserted within the mortise to stop breaking out of the mortise sides). The tenon is inserted, and the mortise dowel gap marked on it. The tenon is then eliminated, and the dowel gap bored, offset barely towards the shoulder of the tenon. A tapered dowel is then minimize 1/8-in. shorter than the dowel gap. When the dowel is inserted, glue is used solely on the ultimate 1/4-in. to stop the dowel from protruding when the piece shrinks.
When pushed house, the tapered dowel wedges the tenon shoulders tightly in opposition to the mortised piece, leading to a joint that can keep extraordinarily tight even when the tenon shrinks away from the mortise sides.
Dovetailed billets
One other movement-accommodating function in Spanish Colonial furnishings is the dovetailed billet. It was a singular Spanish technique for attaching trestles to desk tops. It was not extensively utilized in colonial New Mexico, in all probability as a result of the early New Mexicans couldn’t execute it satisfactorily with their crude instruments, however has change into a normal technique in trendy Spanish Colonial furnishings. It’s made by first chopping dovetail dadoes the width of the desk prime on the locations on the underside the place the trestles connect. A decent-fitting dovetail billet is pushed into every dado, minimize off flush with the edges and sometimes molded. The trestle is normally then hooked up to the billet by hinges, screws, or bolts. Thus the desk prime is free to drift on the billet whereas the legs are nonetheless firmly hooked up.
This technique not solely prevents splitting but in addition controls the cupping tendency of plain sawed desk tops. When the desk prime shrinks, the billet will invariably protrude. An enchancment on the approach is to drive in a brief billet, leaving roughly 1-½ in. of dado at every finish. Then finish plugs approximately 1-⅜-in. lengthy are glued into every finish, leaving shrinkage joints of 1/8 in. To forestall all transferment from accumulating on one aspect, a dowel is inserted by the center of the billet and into the desk prime.
A number of paneling
The following three movement-accommorelationship strategies could be traced on to the Moorish affect in Spain. The primary is a number of paneling. Additionally used on furnishings, this method is commonest in giant door building. The rationale for a number of paneling is as follows: a large panel will shrink considerably throughout its face, thus loosening the panel within the body and exposing the unfinished panel tongue and even the panel edge. A number of panels throughout the identical width will every shrink much less and trigger much less tongue publicity and loosening per panel. Furthermore, the smaller confinement of the wooden provides it much less room to distort on the panel face. An extra function of this frame-and-panel building (and a necessary function on any frame-and-panel) is that the panels are by no means glued into the body groove.
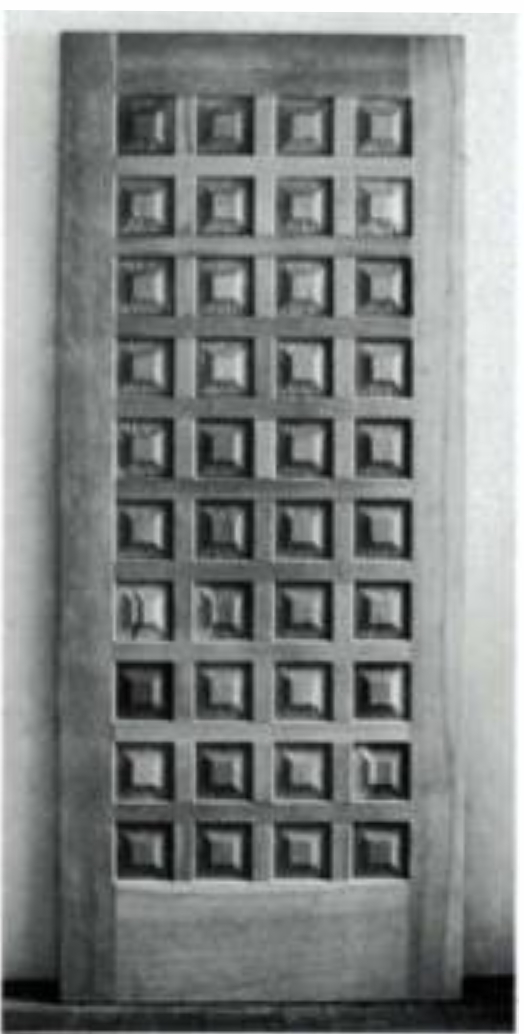
The sheathed door
One other Moorish approach is the sheathed door. It’s made by sheathing a inflexible door body on one aspect with vertical boards. The boards are joined with out glue by a shiplap or tongue and groove joint. Every board is then hooked up to the body on the prime and backside by a nail, screw, or bolt. Thus, every board is held independently and may transfer freely with out affecting the form or look of the door.
Turned spindles
The strategy of changing strong panels with a sequence of turned or shaved spindles can also be derived from Moorish woodworking. Shrinkage within the spindles is inconsequential in comparison with that in a panel, and ordinarily doesn’t have an effect on the looks of the piece. This machine could be seen in cabinets or trasteros, in addition to in sure headboard designs.
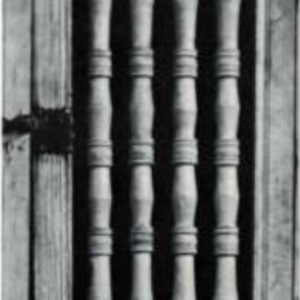

Doweled finger joints
The early New Mexicans generally substituted a doweled finger joint for the normal by dovetail of their chests or arcos. Characteristically they used broad fingers and doweled by just one aspect. A superior joint was produced, nevertheless, in Fifteenth-century Spain, the place the fingers in both sides have been doweled. The ensuing joint held even with damaged glue traces, so long as the underside or prime remained in place.
Butterfly keys
The double dovetail or butterfly key throughout edge joints has come into pretty widespread use in trendy Spanish Colonial furnishings. Though many occasions solely skinny inlaid ornamentation, the important thing can considerably inhibit edge joint breakage attributable to shrinkage distortion when amply made and thoroughly inlaid.
Dealing with edge joints
Cautious edge joint preparation by the Spanish Colonial furnishings maker reduces the potential for joint breakage brought on by shrinkage distortion. (Edge joint gluing is a comparatively latest phenomenon in New Mexico and Spain. Early cabinetmakers had single items of just about any wanted width or thickness, or used an unglued tongue-and-groove joint.)
Typically a spot in an edge joint have to be planed true earlier than gluing although it may be pulled up with clamps. Additional shrinkage could increase the spring and break the joint. Sawed edges are jointed earlier than gluing except extraordinarily clean and straight. If potential, ready edges are glued comparatively rapidly earlier than additional wooden motion distorts the sting line. The glue joint is allowed to dry completely earlier than floor planing or sanding. That is to stop a melancholy from forming on the glue line when the wooden, which swells with the moisture of the glue, shrinks again to its authentic place. If a number of plainsawn boards are glued up, the annual ring arc in the long run grain is reversed alternately, in order that cupping of the person boards doesn’t cup your entire piece.
Select your wooden rigorously
Wooden choice is one other vital facet of the Spanish Colonial furnishings maker’s wooden motion consciousness. An especially standard wooden is the very steady Honduras mahogany. Comparatively steady black walnut and white pine are additionally used extensively. Probably the most movement-conscious cabinetmakers attempt to use comparatively straight-grained material. In addition they attempt to use quartersawn lumber instead of the extra lovely however much less steady plainsawn materials. (Sadly, quartersawn lumber is now virtually unavailable.) Additionally , when laminating, the Spanish Colonial cabinetmaker tries to decide on materials of comparable motion characteristics, matching wooden sorts and avoiding a mix of plainsawn and quartersawn inventory.
Use drying strategies to your benefit
When potential the Spanish Colonial furnishings maker chooses lumber that has had time to air-dry to the ambient equilibrium moisture content material over lumber just lately shipped from the kiln. (The rise of solar-heated kilns could quickly permit lumber yards within the Southwest to dry furnishings wooden all the way down to acceptable moisture ranges, thus permitting production retailers to make use of correctly dried materials.)
Some Spanish Colonial makers use comparatively ‘moist’ wooden to their benefit by making [mortised] items out of it earlier than it dries and making [tenoned] items out of drier wooden. After gluing, the [mortised] piece shrinks to carry the joint extra tightly.
Glue-ups and ending
Many Spanish Colonial cabinetmakers now use artificial glues, most notably aliphatic resin. Nonetheless, some proceed to make use of liquid conceal glue extensively. The low moisture resistance of the glue is much less of an issue within the desert, and its powerful elasticity permits it to face a good quantity of joint motion earlier than breaking.
Motion lodging think aboutations have performed little half within the alternative of finishes. In colonial New Mexico little or no end was used on furnishings. As we speak comparatively low moisture-resistant oil finishes are the preferred. One of many causes for this may very well be that the end on furnishings does little to retard seasonal or longer moisture content material modifications, and shorter modifications have an effect on the wooden moisture content material insignificantly. One rule of furnishings ending nearly universally adopted by the Spanish Colonial cabinetmaker is to complete each side of any board liable to cup, and to make use of a end with comparable moisture-resistant qualities on each side. A closing conventional rule of the Spanish Colonial cabinetmaker is to keep away from endbanding of strong inventory if in any respect potential. Not solely does it result in an unpleasant overhang of the top band, however it is going to break the banded plank if secured tightly at multiple level.
Not only for westerners
The Spanish Colonial cabinetmaker is in some ways the current embodiment of a protracted and interesting custom of furnishings making. However, the movement-accommodating strategies which have developed as a part of that custom shouldn’t be of interest solely to the desert cabinetmaker. Wooden strikes with the temperature and humidity of the air round it. In a New York Metropolis house which is heated within the winter and open in the summertime, wooden moisture content material could change greater than within the desert. Few cupboard makers know whether or not the lumber they use is at its equilibrium moisture content material, or whether or not the furnishings they construct will probably be moved to a markedly different local weather. For these causes each cabinetmaker, it doesn’t matter what fashion of furnishings she or he produces, should make design and execution selections with the potential for wooden motion in thoughts. The historical past of Spanish Colonial furnishings building can supply useful strategies helpful in minimizing the results of that motion.
Join eletters immediately and get the most recent strategies and how-to from Nice Woodworking, plus particular affords.